AUSTIN, Texas — It’s lunchtime at Amazon’s AUS2, a six-story warehouse set between housing subdivisions and a state highway on the edge of vast farmland just outside this city’s famous limits.
With a footprint bigger than the Texas Longhorns football stadium, this 2-year-old, 11th-generation robotic fulfillment center employs 3,000 people and holds 35 million units in inventory, buzzing with activity for much of the day.
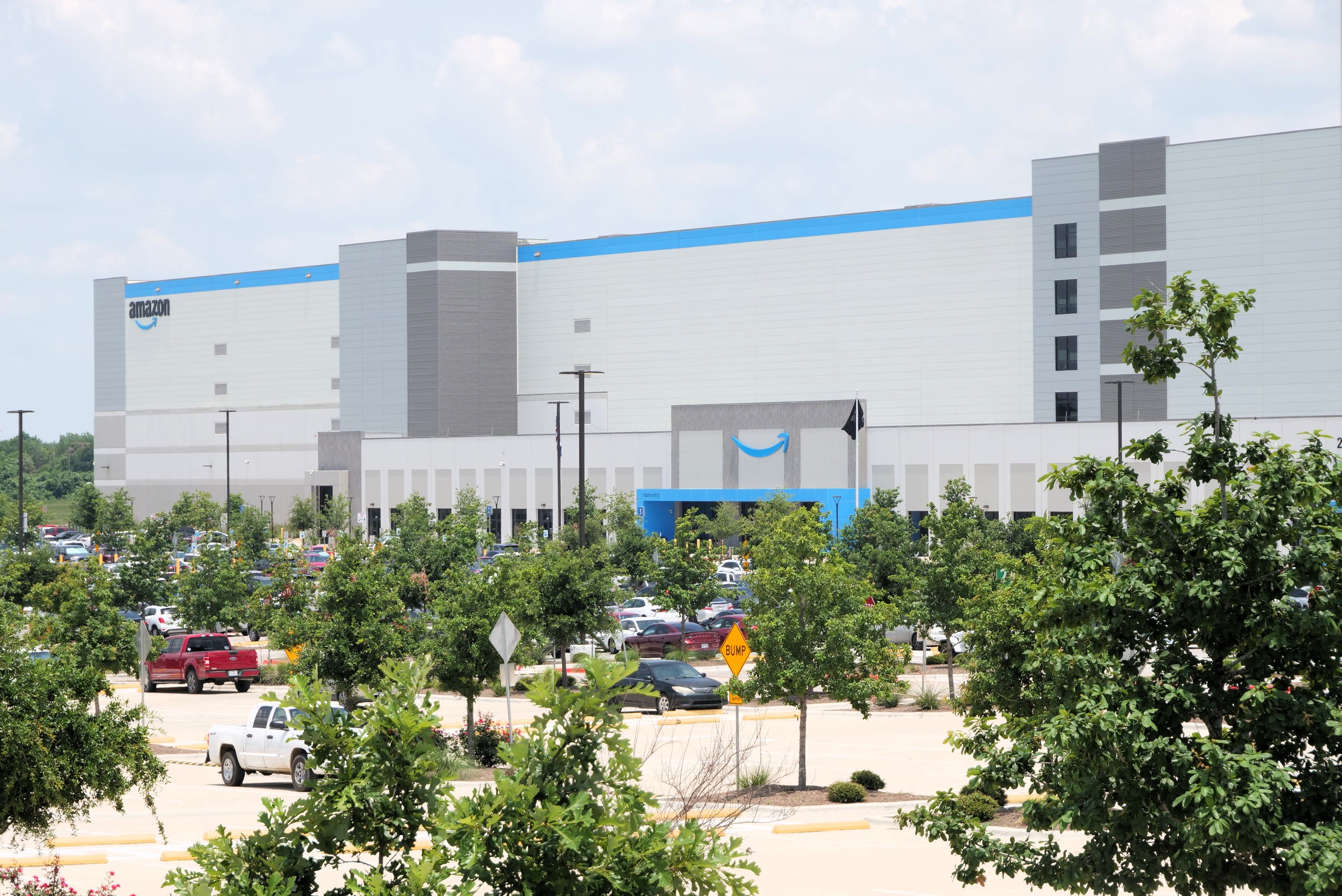
But as Amazon’s employees take a break, another group is still hard at work: Amazon’s Robin automated arms and Pegasus mobile drive units.
Robots don’t stop for lunch.
The yellow Robin arms identify packages using an array of cameras and sensors. They use high-tech retractable suction rods, in varying combinations, to pluck and place boxes and bags onto the blue Pegasus platforms.
The knee-high robots zip around in a computerized choreography, navigating via QR codes in the slate floor and using their little built-in conveyor belts to send packages down the designated chutes.
In the past, this work did not happen at Amazon fulfillment centers, where the primary tasks are putting products in packages, and labels on them. Traditionally, these packages are then routed via separate Amazon sortation centers, which then send them to the delivery stations responsible for getting them to customers.
The duo of Robin and Pegasus replace that intermediary stop.
There are nearly 40 Robin arms in this facility, part of a fleet of 1,000 of them deployed in the company’s warehouses across the country. Collectively, Robin robots handled about a billion packages last year, Amazon says, or more than 12% of the company’s total package volume over that timeframe.
These types of robots raise all sorts of questions about the future of work. A few years ago, before the pandemic and the rise of labor shortages, they might have created more concern about job loss.
But increasingly, Amazon is counting on robots to help make its warehouses safer.
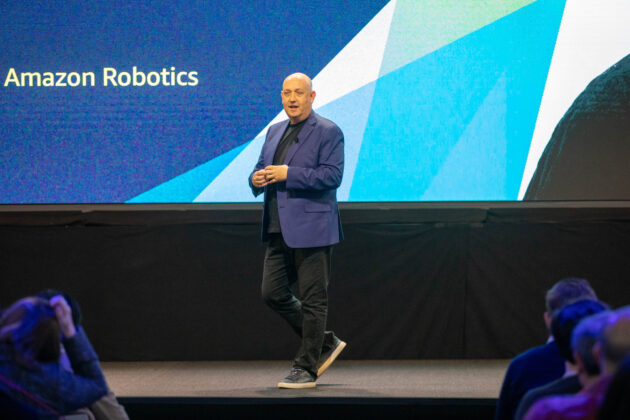
“We really index on reliability, on quality, on scale, and most importantly, on safety,” said Tye Brady, the chief technologist for Amazon Robotics, describing the company’s approach in a recent interview.
The idea, he said, is to “eliminate the mundane, the repetitive, the tedious,” freeing up humans for higher-level work with less risk of physical wear and tear. “The more that we can pick up objects, sort objects, and put them into boxes automatically, the better it is for everybody involved.”
Amazon’s safety controversies
Safety is top of mind for others, as well. Federal and state regulators, labor unions, and Amazon shareholders have repeatedly raised red flags about Amazon’s warehouse injury rates. A few examples:
- In Amazon’s home state, the Washington Department of Labor & Industries recently cited a fourth Amazon facility for requiring workers “to execute repetitive motions, lifting, and other physical work at such a fast pace that it puts workers at risk for developing Work-Related Musculoskeletal Disorders.”
- A widely cited 2019 report by the Center for Investigative Journalism showed a higher injury rate at Amazon’s robotic fulfillment centers than at its older facilities at the time, indicating that human workers were struggling to keep up.
- A report by the union coalition Strategic Organizing Center, released in April of this year, asserted that Amazon’s “serious injury rate” was more than double the industry average.
Amazon disputes and denies these claims. The company, famously willing to be misunderstood for long periods of time, would see this as yet another example.
In a case that resumes later this month, Amazon is appealing the first three citations by Washington L&I, at facilities in Sumner, Kent, and DuPont, Wash., and dismissing as “categorically false” the agency’s allegation that the fourth citation, in Spokane, amounted to a willful violation.
In almost every other situation, Amazon takes issue with the numbers.
“Having spent some time with the safety data myself, there are a lot of ways you can spin that data and there are special interest groups that regularly skew them for their own agenda,” said Amazon CEO Andy Jassy at the company’s 2022 annual meeting, when a shareholder asked what he was doing about safety.
Releasing its annual safety report in July, the company said claims that its injury rates were significantly higher than the industry were based on misleading calculations from “outside groups with ulterior motives,” wrongly overlooking data from its peers and counterparts such as Walmart, Target, Costco, UPS, and FedEx.
“[S]ometimes we’re higher, and sometimes we’re lower than other companies, but to paint us as significantly worse than the rest of the industry simply isn’t true,” the company said in its July post. “At the same time, our goal isn’t to be average—we want to be best in class compared to our peers, and we are optimistic about our continued progress so far this year.”
Amazon maintains that robots will help. The company cites its 2022 safety data as an early indicator. Numbers provided by the company show that recordable incident rates and lost-time incident rates were 15% and 18% lower, respectively, at Amazon Robotics sites than they were at its non-robotics sites in 2022.
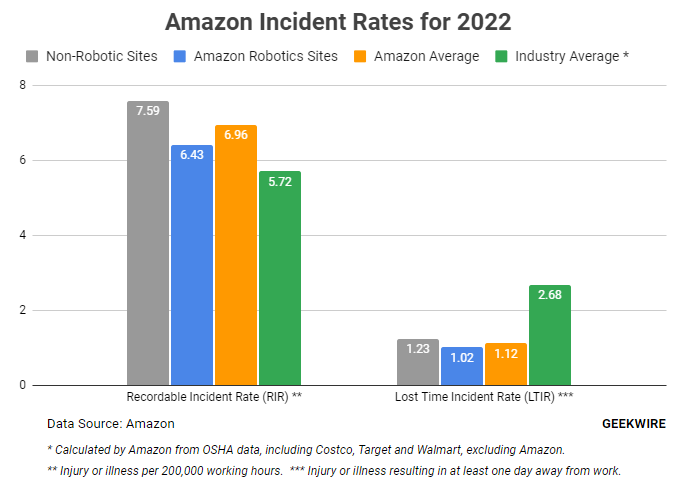
Amazon didn’t provide the number of robotic and non-robotic fulfillment sites used in the calculations, which would make the sample sizes clear. The company also hasn’t publicly broken out the difference in injury rates at its robotic and non-robotic sites for prior years, which would provide a sense for the trend over time.
Amazon’s robotic boom
But there’s no question that robots are doing more and more of the heavy lifting at Amazon fulfillment centers, as GeekWire saw first-hand during tours with site leaders at facilities in Austin and San Marcos, Texas, this summer.
It starts with the “Hercules” robotic platforms that deliver shelving units to workers at fixed workstations, eliminating the need to walk the floor to pick products. Amazon says there are now more than 750,000 of these units across its operations, an evolution of its acquisition of Kiva Systems more than a decade ago.
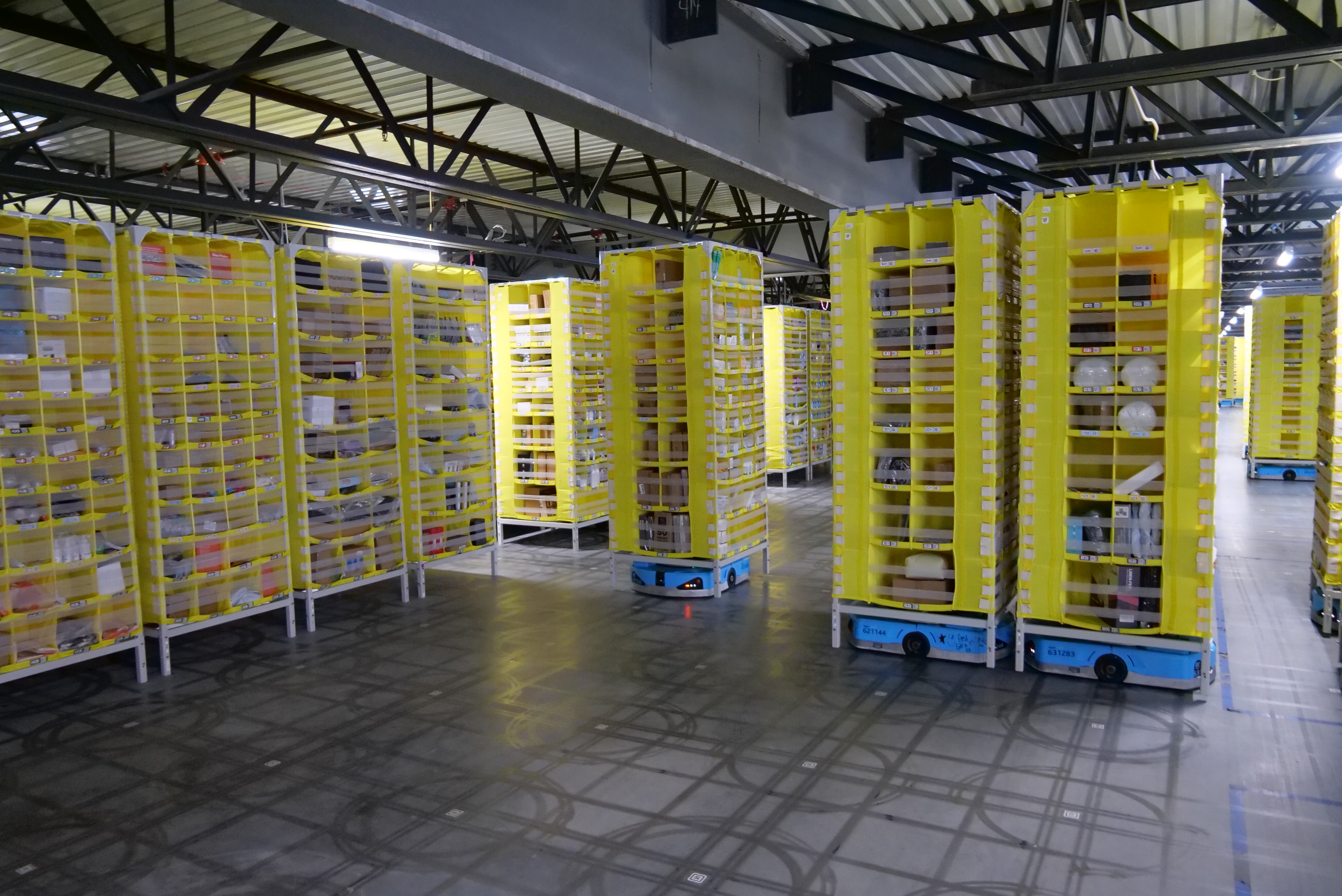
That change alone has been dramatic, said Robert Morua, a senior operations manager at AUS2, who recalled what it was like when he started 13 years ago as a front-line worker in a traditional Amazon warehouse.
“As a picker, I’d walk 20 miles a night picking products,” Morua recalled. “Here, the picker is standing in one spot, and all the product comes to the picker. So we’ve severely reduced all that walking, and all that wear and tear on the body.”
Even so, Amazon workers remain at high risk of ergonomic hazards and musculoskeletal disorders due to the fast pace of work, long hours, the heavy weight of items, awkward twisting, bending, and extending of their body, the U.S. Occupational Safety and Health Administration has found in a series of investigations at Amazon facilities.
Amazon says it’s making ongoing efforts to reduce injuries through process improvements and changes in the designs of its workstations, with the goal of improving efficiency and safety.
Examples from our Austin tour included basic upgrades such as the introduction of ergonomic ladders, and high-tech solutions such as software that stops associates during scheduled windows to lead them through stretching routines specific to the work they’re doing.
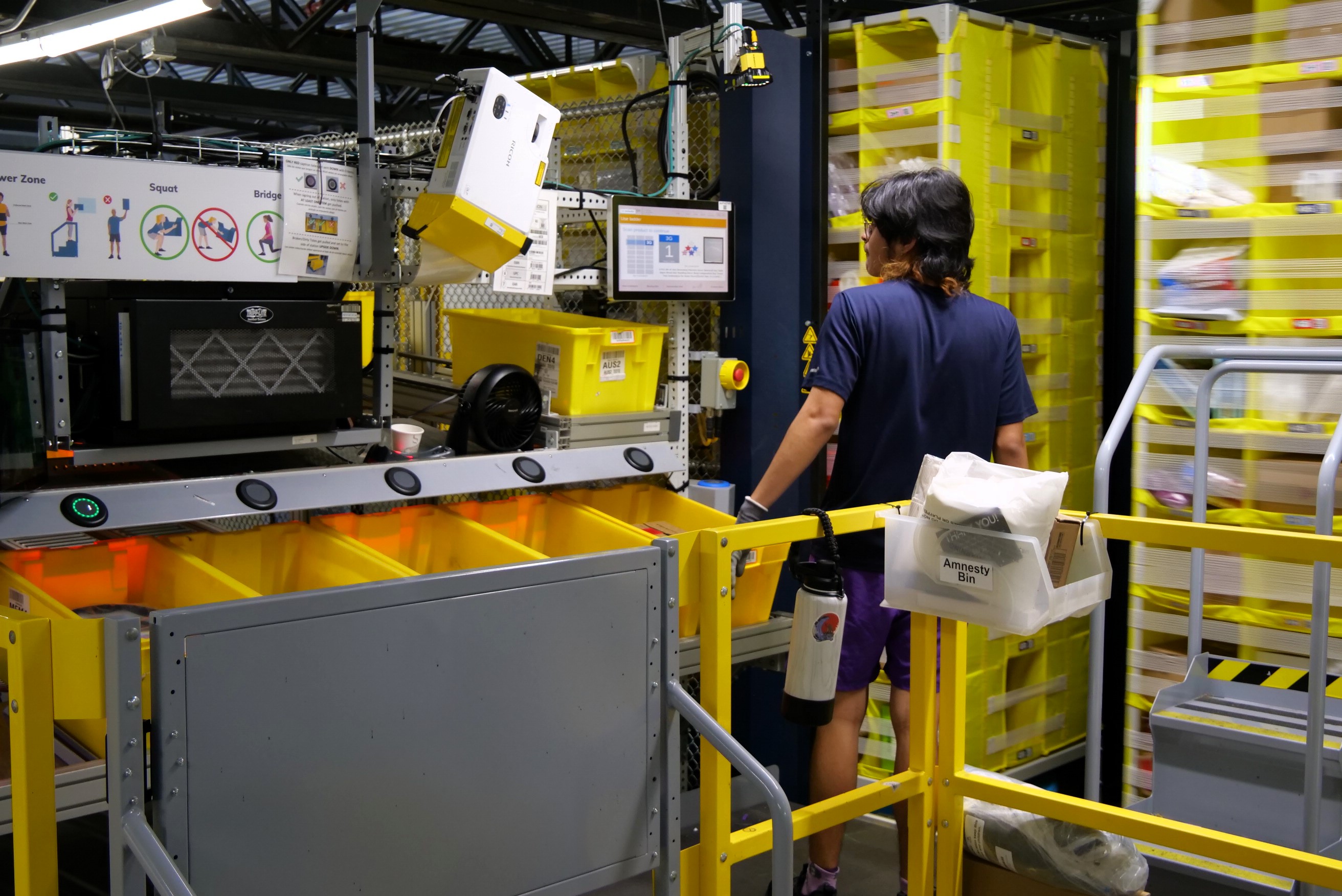
Workstations are equipped with lights that shine on individual bins in the fabric shelving units carried by the Hercules drives, showing workers where to place specific items. The system is programmed to prompt the associates to put smaller, lightweight items in the higher shelves, leaving heavier objects for shelves in their power zones.
“One of the biggest things we’ve worked on is reducing MSD [musculoskeletal disorder] injuries,” said Dom Gutierrez, the AUS2 workplace health and safety manager, pointing out some of the changes during our tour.
Beyond ergonomics, some safety regulators are also focusing on the risk created by noise levels in Amazon facilities. Washington L&I’s latest Amazon citation, for example, included allegations of “three serious and one general violation for noise levels that were too high when workers are not wearing appropriate hearing protection.”
Before stepping onto the floor at AUS2 as a visitor, I was given a high-visibility safety vest and required to put on special shoe covers with reinforced toes. However, there was no requirement to use any ear protection.
The noise from the high-speed conveyor belts was so loud at times on the tour that it was difficult to hear the Amazon site leaders, even from a close distance. They provided short-range wireless radios with earpieces to communicate.
Latest robotic advances
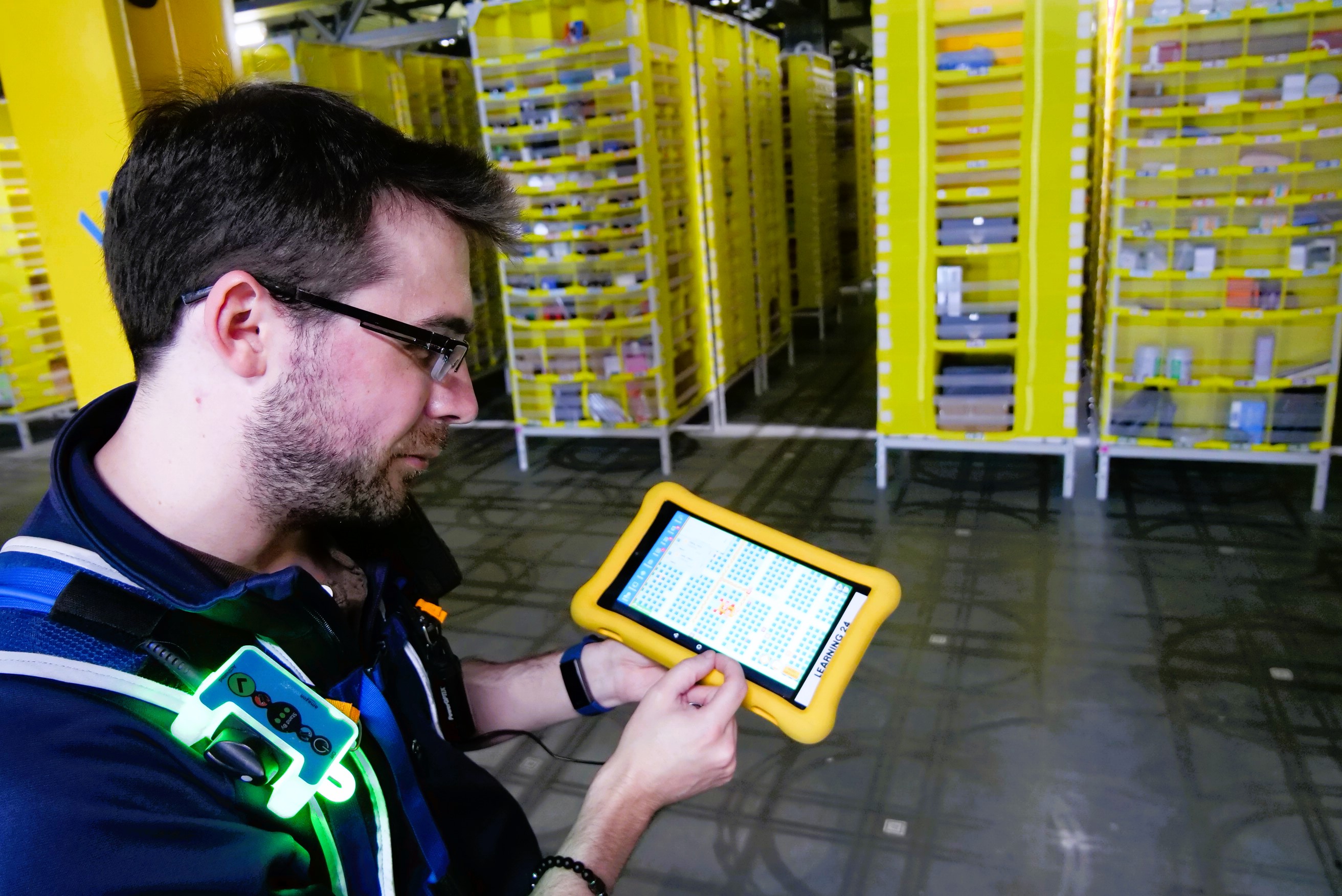
The introduction of robots has also created safety risks that the company has taken steps to address. Many of its existing robots operate behind fences to reduce the risk of unsafe interactions with workers.
The technicians who go behind the fences to work on Hercules drives, for example, wear special safety vests that send out radio signals causing the drives in their vicinity to stop moving when they’re in close proximity.
Elsewhere in the Austin facility, a large robotic arm puts containers of items onto pallets, surrounded by an invisible light curtain that automatically stops the arm from moving when someone moves into its work zone.
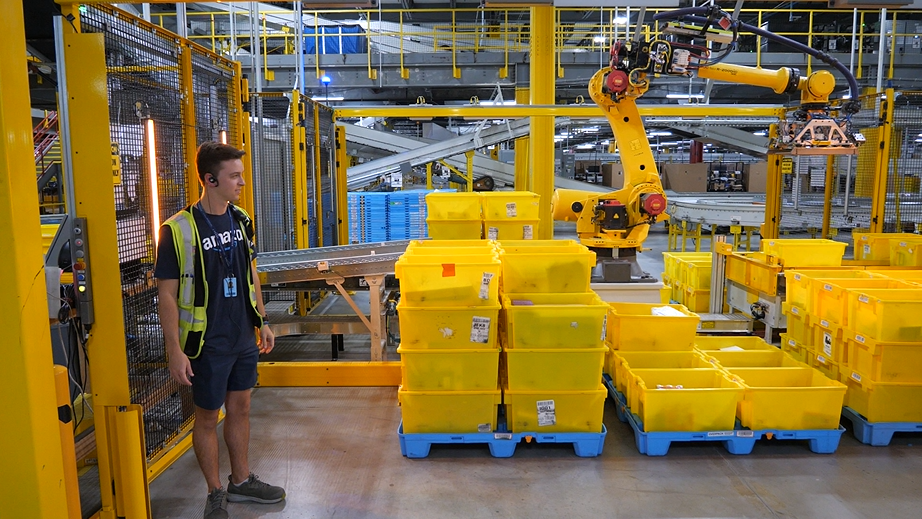
Amazon last year unveiled a new mobile drive unit, dubbed Proteus, that the company describes as its first fully autonomous robot designed to operate safely alongside humans on the warehouse floor.
Other new robots in the works promise to further reduce the risk of injury from repetitive motion.
- University of Washington researchers, working in an Amazon-funded lab, are testing a prototype robotic arm to remove items from the fabric pods. This was visible in a short video clip posted by U.S. Sen. Patty Murray’s office after visiting the UW’s Allen School of Computer Science & Engineering in August.
- Amazon is expanding its testing of Sparrow robotic arms, its first automated robots in the field that can grasp individual products of varying shapes and sizes, not just packages and boxes. Amazon says Sparrow can handle about 65% of the more than 100 million items in its inventory.
- Amazon says it will begin field testing a new robotic system for containerized storage this fall at a facility in Houston. Unveiled last year, it’s designed to reduce the need to stoop, reach up, or climb ladders to retrieve or stow products, bringing the containers to workers in their “goldilocks zone” around the midpoint of their bodies.
Brady, the Amazon Robotics chief technologist, said he believes the company’s applied robotics — developing and deploying automated technologies, at scale, to solve real-world problems — will ultimately have implications beyond Amazon, influencing other industries.
He said this is what motivated him to join the company eight years ago.
“It’s not humans against machines,” he said. “It’s humans and machines working together to do that task, and we’re pioneering that movement.”
Coming Up: Tye Brady, Amazon Robotics chief technologist, will be the guest on this week’s GeekWire Podcast, available Saturday morning. Subscribe in Apple Podcasts, Google Podcasts, Spotify or any podcast app.