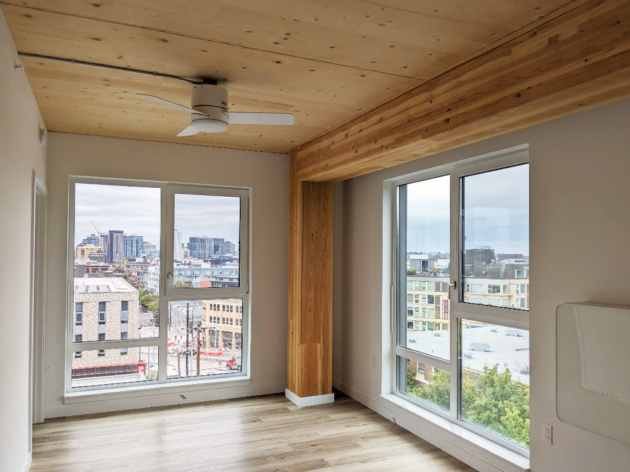
When Seattle’s eight-story Heartwood Apartments opens to residents this fall, it will be Washington’s tallest timber building and the first in the U.S. permitted under a set of new construction codes that allow for wooden high-rises up to 18 stories.
It’s a significant milestone in America’s shift toward mass timber as a lower-carbon alternative to concrete and steel, and the Pacific Northwest is helping lead the way. Seattle architect Susan Jones is a pioneer of the U.S. movement, spearheading the creation of the new codes and demonstrating the technology’s potential.
“There’s so much room for innovation and design with this new emerging material.”
– Susan Jones, owner of the architectural firm atelierjones
“There’s so much room for innovation and design with this new emerging material,” said Jones, owner of the architectural firm aterlierjones, which designed Heartwood and other mass timber buildings. “I’m really excited about the future.”
Wood has been a building material for as long as humans have constructed shelters. But over the 20th century, concrete and steel dominated as buildings became massive and soared skyward. Now wood is being engineered into products with enough strength and fire resistance to create the backbone of tall structures.
Nationally, 69 mass timber projects were built in 2013 — a number that spiked to 755 by last year, according to Bloomberg.
The wood frameworks are on display in dozens of public and commercial buildings in the Pacific Northwest, including the University of Washington’s Founders Hall, the Portland International Airport, the Muckleshoot tribe’s smokehouse and the La Conner Swinomish Library. There are residential efforts as well, including mass timber homes from Seattle company Green Canopy NODE.
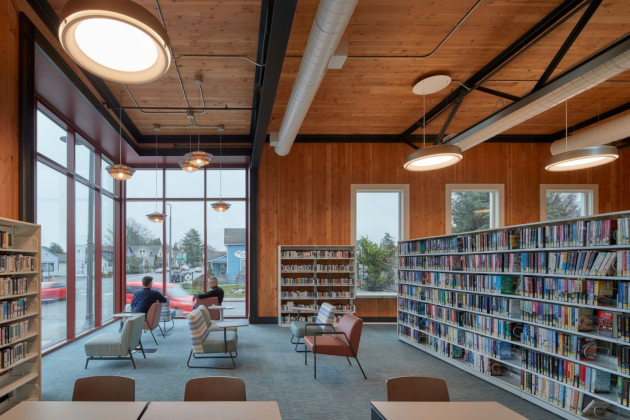
“Building on Washington’s historic strength in forestry and timber, advanced manufacturing and the substantial numbers of innovative architecture and construction companies here, we believe the state is ready to expand its leadership in the production and use of mass timber,” said Brian Young, clean technology lead for the Washington Department of Commerce, by email.
The expansion aligns with the state’s ambitious climate goals. The building and construction industries are responsible for 13% of global carbon emissions — largely due to concrete and steel. These sectors are trying to decarbonize, but it will take time.
Researchers have calculated climate benefits from using mass timber, though critics argue they’re overblown. Growing trees help the climate by consuming carbon and the lumber locks up the planet-warming gas for the life of the building, or longer if the wood is later reused. The wood that’s turned into mass timber typically comes from forests managed for harvest, not old-growth trees.
Research on the Heartwood project by the University of Washington, Pacific Northwest National Laboratory and others concluded that its carbon footprint was 40% less than a comparable build using steel and concrete, with additional benefits over time from the stored carbon.
Fire resistant and quake safe
Europe has been building with mass timber for the past couple of decades, but winning support in the U.S. has been challenging.
There’s a learning curve for builders and contractors to develop the skills needed for building with the material, which can add time and costs to a project. Domestic manufacturers only recently began selling mass timber products. There are still some code restrictions and permitting might take longer. The materials often cost more.
And at least historically, builders and permitters worried about mass timber’s performance, with fire safety at the top of the list. To gain approval for the new building codes, Jones served on a committee tackling fire resistance issues. At a national fire research lab, the group tried five times to burn down full-scale, two-story mass timber buildings.
“It didn’t work,” Jones said. “Four hours of fires. No sprinkler intervention. No fire department intervention. Really amazing.”
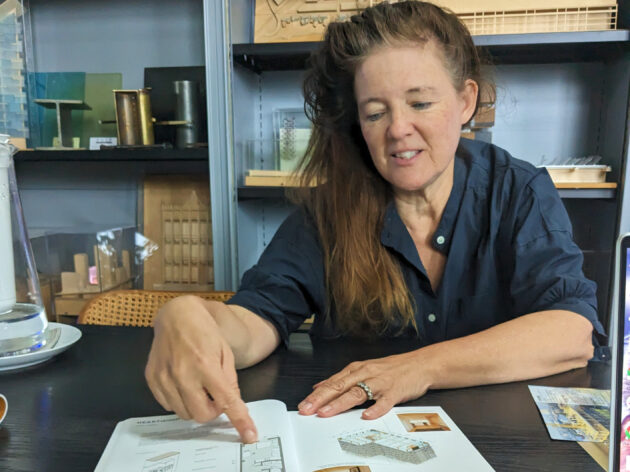
When mass timber products are exposed to fire, they form a protective layer of char that slows the burning and retains the structural integrity of the wood.
More recently, scientists researched mass timber’s seismic integrity. They built a 10-story mass timber tower and subjected it to the equivalent of 150 quakes at a test site in San Diego. The tests were completed in August and included researchers from Washington. The building came through “without structural damage or residual deformation,” according to the project website.
And mass timber projects aren’t solely wood, but rather hybrids that often include steel and concrete in a limited capacity. For structures like expansion bridges and skyscrapers, metal and concrete will still prevail.
“What we need to do for our collective sustainable future is stop relying on [steel and concrete] as the base material and use renewable resources,” said Bec Wilder, co-CEO of GreenCanopy Node. “Where can we replace it with wood, let’s replace it there.”
Wood skeleton on display
From the outside, the Heartwood Apartments look like a typically modern high-rise in Seattle’s Capitol Hill neighborhood.
But the building has a skeleton made of mass timber, and inside its bones are proudly on display.
Exposed burly wood beams run horizontally along the ceilings and wood columns stretch from floor to ceiling in most of Heartwood’s 126 studio and one-bedroom apartments. The beams are a glued laminated timber, or glulam, constructed from lumber that’s bonded together.
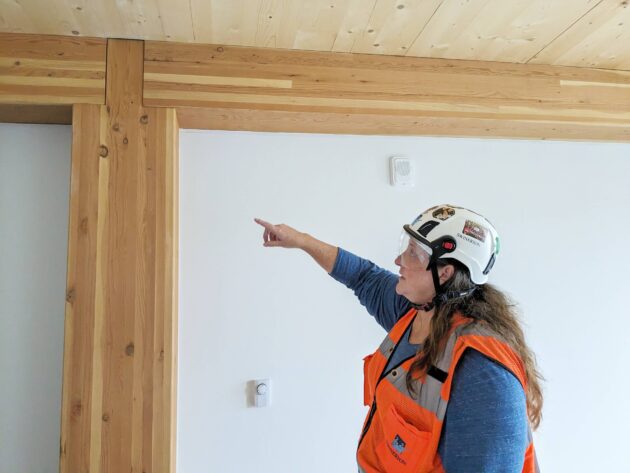
There are also exposed ceilings of cross-laminated timber, which are wood panels made from boards that are stacked so the wood grain alternates direction with each layer and then are bonded together.
In addition to the mass timber, Heartwood has an internal lattice of concrete-filled steel beams that provides further seismic support.
Atelierjones designed the project, which broke ground in April 2022 and is constructed by Swinerton. The nonprofit Community Roots Housing owns the building and manages it via a third party. It will rent to medium-income households. Studio units will go for $1,326 – $2,075 per month and include access to shared laundry and bike storage rooms.
Last week prospective renters began touring completed units.
‘Mass timber rising’
Elsewhere, other mass timber projects are taking shape.
This past spring Green Canopy NODE erected its first mass timber home in Spokane that was assembled using prefabricated panels. It partnered on the project with Mercer Mass Timber, a Vancouver, B.C. company that acquired Katerra’s operations in Spokane after the latter went bankrupt.
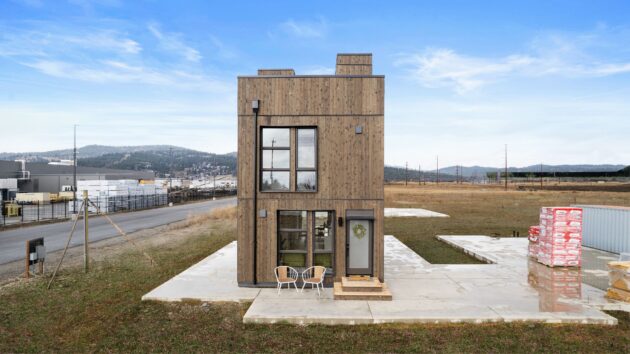
Green Canopy NODE’s niche is mass timber homes under four stories with a focus on housing that is carbon negative and quick to build. It’s currently selling prefabricated mass timber homes to developers building multi-unit projects. Next year it’s erecting a 32-unit mass timber apartment building in Seattle’s Rainier Beach neighborhood.
Wilder, the co-CEO, sees a ton of potential in the space, citing multiple reasons:
- New mass timber manufacturers are coming online, allowing for projects to be locally sourced.
- The material is attractive because it can be ordered to precise, pre-cut measurements that reduce waste and can, in the right hands, speed the time of assembly — both of which also cut costs.
- The mass timber is lighter than steel and concrete, so costly excavations and foundations can be scaled back.
While mass timber has been more expensive, these factors are bringing it closer to parity with traditional materials, Wilder said.
We’re still in a “nascent time of mass timber rising,” they said. “But it’s huge. We’ve got a mass timber conference, and a couple years ago, there were 1,000 people there. And last year, there was 3,000 people there. It’s just growing awareness of the material, [and] how to use it.”
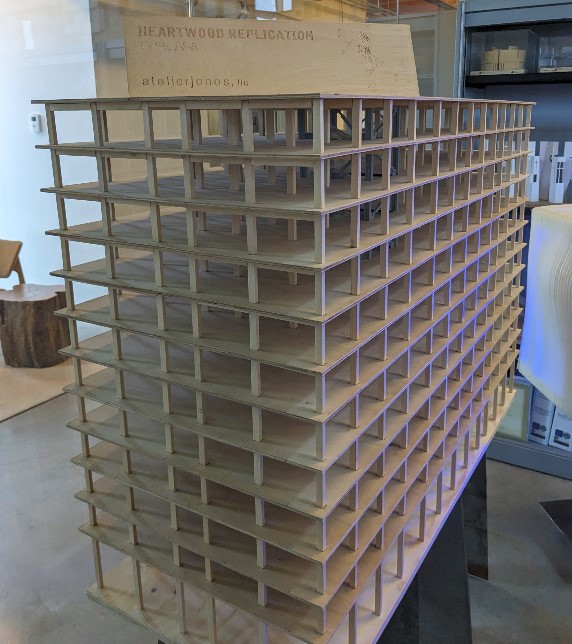
From home to Heartwood
Jones’ advocacy for mass timber literally began at home.
In 2013, she built her family’s Seattle home in Madison Park from mass timber as an experiment and opportunity to learn about the material. It was a risk, but one she wanted to take to demonstrate to herself and others that mass timber was a viable technology.
“To learn how to build with it through that process was invaluable,” Jones said. “It really became the prototype for all of our work for the past decade.”
Jones grew up in the Pacific Northwest and loves the warm esthetic of wood construction, a fondness she traces back to a family cabin on Orcas Island.
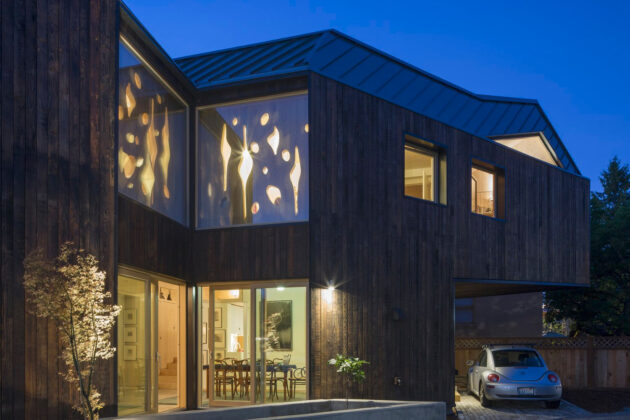
Since building her home, atelierjones has designed mass timber projects including a school, a church and residential housing — which includes modular replacement homes for residences destroyed in California’s 2021 Dixie Fire.
Now that her firm has done the hard work of making the eight-story Heartwood building a reality, Jones wants others to follow suit. She’s working to replicate the apartment’s design on a larger scale, for buildings 10, 12 and 18 stories high. Jones expects that mass timber buildings reaching 40 stories are possible.
“The 20th century got us off track,” Jones said. “And I feel like the pendulum is swinging back to a more nature-based bio-based materiality of the way we live.”
Editor’s note: Story has been updated to reflect Bec Wilder’s last name change from Chapin.